Interview Sarah MacLeod
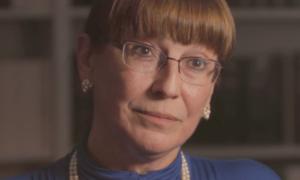
"You can't fly an unairworthy aircraft, so part of your business is obviously to keep airworthy aircraft," says MacLeod, executive director of the Aeronautical Repair Station Association, an organization that represents aircraft repair stations worldwide. "But if I can have you do it more efficiently, it's kind of foolish for me not to." This is the edited transcript of an interview conducted on Nov. 9, 2010.
Read ARSA's response to our program here.
My introduction to this business in vivid detail was going to this convention in Phoenix. Were you there?
Yes.
... What was that convention all about? What goes on at that convention?
Well, you went to MRO Americas, and that is run by Aviation Week, and it is an opportunity for the customers to sit down with their vendors -- so the airlines to sit down with their vendors -- and also for repair stations to sit down with other repair stations and develop business relationships or to confirm business relationships or to establish auditing criteria for the year and introduce new concepts or new products. It's a trade show for aviation maintenance providers.
This is a thin margin business?
Especially in the airframe business, yes. You can have heavier margins in components and specialized repairs, welding, coatings, special services.
But when you're talking about the heavy checks --
Yeah, the heavy checks are not a big-margin business.
Is it a good business, though?
I wouldn't want to be in it.
Well, you kind of are, aren't you?
No, fortunately. I get to represent people for regulatory compliance purposes. We're just recently getting into the economics of the industry. We were trying to keep the regulator and the regulated on the same page so that there wasn't misunderstandings and so that we could keep our safety record as high as we possibly could, and also to improve. Remember, the Federal Aviation Administration, for the most part, sets minimum standards, and it's up to the industry to make certain that we're above that....
Give me a kind of 101 definition for somebody who doesn't know what an MRO is. What is it?
A repair station.
MRO stands for what?
An MRO is a redundant term. It stands for maintenance, repair and overhaul, and if you look at the definition of maintenance in almost every regulator, it includes repair and overhaul.
Just trying to define what these shops are. What do they do, and what do they sell? You say MRO; what's going on there?
Yeah. So if people would -- jeez, I hate to really bring it down to a car level, because it is different than pulling --
Car level is OK. That's about where I am, so that's good. ...
It is a little bit different than pulling a car into the garage.
Try it anyhow.
OK. So you pull your car into the garage for a heavy check. That means something really went wrong for you, so ... for most of us, we wait until something goes wrong. In the airline industry, I have to have a continuous airworthiness maintenance program. Not only do I have to fix things that break when they break, but I also have to be looking at things all of the time, inspections, and I also have to replace things on a regular basis. Those are my time-life parts and my hard time items.
So I, as an airline, say I want to replace my landing gear every 5,000 hours, which is not what they do but it would be an example. I can choose things that I hard time, and that's usually based on reliability and safety or the redundancy of the system.
So I'm an airline, and I have to have regular maintenance; I have to have regular inspections and regular maintenance. So I hire somebody like a TIMCO [Aviation Services] to do my heavy checks. When it's in there, I remove and replace a lot of components, so when I remove those components, those will go to accessory shops or landing gear shops. They'll go to specialty shops. I remove the engine. Sixty percent of the time I send it back to the manufacturer to repair.
OK. So what we're talking about here is rules which say as a plane gets older, at certain periods of time, you have to do XYZ to it. Whether it is working or not is irrelevant, right?
Correct.
And so these shops are, from large to small, [they] address either the full airframe all the way down to a piece of avionics or whatever it may be.
Or coatings. So I have aircraft -- unfortunately, the United States has called airframe but really aircraft maintenance, completed aircraft, completed engines, completed propellers, and then I have components. And in the United States, again, we made it a little bit more complicated -- instruments, radios, accessories -- and then you have specialized service -- welding, coatings, braising.
All right. So this business -- if I'm running an airline, and I have a 737, pretty much everything I need to get done in maintenance I can find a shop to do it, right?
Correct.
I don't have to do any of it myself.
Correct.
And the airlines have been doing more and more of it this way. Why are they interested in outsourcing this work?
Contracting. When you say "they," we are actually looking at legacy carriers, because as you know, the more successful airlines didn't start out with the in-house capabilities to begin with. And also the package carriers didn't do a lot of in-house maintenance. Most of them do line maintenance. So what I would look at is what business am I in. Am I in the business of flying passengers or cargo, or am I in the business of maintaining my fleet?
So I think that's one of the things that we actually look at in almost all of our industries is what business -- you know, we came up with this term, I don't know, five or six years ago, "core business," so I think they are starting to look at that a little bit more seriously. They're experts at flying aircraft and conveying passengers, so I think they started looking at that. And I think that the Southwest -- Mr. [Herb] Kelleher -- looked at that from the very beginning.
And Southwest from the beginning outsourced its maintenance?
It arranged to have its maintenance performed by the specialists in the industry, correct.
You don't like that term, "outsourced," do you?
I do not.
Why not?
Because I'm more precise in my language than most people are, and it's a contract, and I think that we need to take contracting seriously, and I think there's obligations under contracts that we need to comply with, and "outsource" is a throwaway term to me.
... Well, a lot of people would say using these shops is a shortcut. ... Isn't it?
No, sir. I think it's using the people that are most capable of performing the service that you are required to perform. It's kind of like saying that you need -- if you buy a car, you have to repair your own car. I think that in the world and in the United States, we have choices, and we make it based upon much more in-depth and intelligence than throwing terms at it. Otherwise we can't be successful. Now whether we are or not sometimes has to do with luck and other things.
But what Kelleher and Southwest discovered is this [would] save them money, save the airline money. It was cheaper to do it this way, right?
Remember when he came out, he said "competed with the car." ... And in order to do that, I have to have the same kind of fleet. I've got to uniform my fleet so I can cut down on the cost of training my pilots and I can turn my fleets in 12 minutes, because remember, that was the other thing he was doing, is gate turns. And he looked at what it would take to be successful at transporting people by air. And I think one of the questions he had to ask himself was, "Do I put all of this cost of doing business" -- because the barriers of entry into maintenance are very high -- "do I put it all in -- do I put a portion of my money into that, or do I take that money and provide a uniform fleet and some other things that are more important to me for transporting my passengers?"
And the answer was --
"I will let the specialists do the maintenance for me, and I'll fly my aircraft."
So somebody else does the maintenance. Just like you go to the garage to get your car fixed. All right. What's interesting, though, we've seen the so-called legacy carriers, the old-time airlines, if you will, move in this direction as well. And what's interesting about that is they already have made that investment in maintenance, in some cases a huge investment in maintenance and a lot of skilled personnel. ... Sixty or 70 [percent] of United, I think thereabouts, is now outsourced. What's going on inside United? Why are they shifting if they've already made this investment?
It's kind of interesting, because they also started UAL Services, [United Services, a full-service global MRO provider], so they looked at their expertise --
Let me ask the question again. I get it when you talk about the Southwests or the JetBlues of the world, starting with a clean sheet of paper in this day and age, why they would not want to make that investment upfront. But when you look at the legacy carriers, the old-time airlines, if you will, that have already made that investment in maintenance, personnel and expertise and everything, moving toward outsourcing -- there must be something motivating them. What is it?
... They're in competition with the people that did get to start with a clean slate. That's one thing. And the other thing is, if you'll notice with American and UAL Services -- sorry, United Services -- they have decided to take their expertise, the things they were really good at and they really did invest in and didn't have to continue to invest in as they change their fleets, because remember, I can invest, but I also am going to have to do a continual investment in tooling and equipment and bigger hangars if I'm going to use bigger aircraft. So it's not just the first investment; it's the continuing investment. So ... can I also make money from that? And that's where you take a look at people like Lufthansa.
In l994, when the Europeans said U.S. airlines are not going to be able to perform maintenance on your own aircraft without a Part 145 certificate; [that] you have to get a repair station certificate, [and] the only people that can perform maintenance on airline aircraft in Europe are Part l45 persons -- when Lufthansa was faced with that decision, it became Lufthansa Technik, and it took its expertise that it got from its own airline experience and turned it into a business.
And I think United and American are trying to do the same thing, and Delta TechOps. You see, they also turned it -- because this is America, we can make lemonade out of lemons, they've also tried to turn their expertise and to serve the world. And it's a very important aspect of their knowledge that we don't lose, the individuals as well as the companies.
So when they took a look at it -- I mean, some of them did cut their losses. Well, I'm not an expert in -- not sure the airlines an expert in airline economics -- but part of it is you really have to take a look at what the demands of your market are. So Southwest came in and said "Cheaper flights" and "I can," "No thrills" -- I keep saying that -- "No frills," so that was...
And hopefully no thrills, either.
The thrill was when you came to the airport, right? In the taxicab.
Right. That's the goal. ... What is it that makes it cheaper for the airlines if they go to an outside maintenance provider?
The simplest way for me to kind of put it in a nutshell is that investment that I've made in my hangars and my backshops and all of that, if I take it to somebody that does that for a living and keeps that hangar full or the backshop full, I'm not spending money on training and people not working 100 percent of the time, not being -- I know this sounds kind of negative -- but not being productive 100 percent of the time. I'm just working on my product. It's kind of hard to keep my shops and my hangars full all the time. But if I take it to a specialist in the area, I'm going to be competing, if you will, with other customers, but I've got a contract with that person that says this is what you're going to do, and this is the time frame you're going to do it in. And I can choose that time.
Are you telling me that an airline like Delta, American, United and all the airplanes they have can't keep their shops busy on a regular basis?
Remember, they weren't Southwest. They have different fleet types, and each one of those takes different expertise in different specialties, and the overhead for those legacy carriers that started out 50 years ago or so, they carried a lot of baggage with them into that new era, so no, they couldn't do it as efficiently or as effectively. It's not their core business. Their core business is to fly aircraft; it's not to maintain a fleet. That's why they are now -- if they could take care of their entire fleet, then why do we have Delta TechOps at all? They've obviously taking up extra capacity with customers. And American and United.
Their core business is to ensure a safe trip, isn't it?
… Absolutely. But that's a given. I'm not going to stay in business very long if I'm going to be crashing aircraft. Their core business is to fly aircraft. You can't fly an unairworthy aircraft. Miles, you know that; you're a pilot. You can't fly an unairworthy aircraft, so part of your business is obviously to keep airworthy aircraft. But if I can have you do it more efficiently, it's kind of foolish for me not to.
Where are those efficiencies, though? Is it just that workers are paid less?
No, it's because we have specialty and core centers. I don't know if you noticed this at the MRO, but if you have Airbus aircraft, you go to one business; if you have Boeing, you go to another. I mean, we specialize in a particular fleet type, manufacturer or fleet type.
And if I were to go in there, the work would be done exactly the same way as it would be in-house, so to speak?
Correct. The airline obviously directs the work, but the airline can also take advantage of the knowledge that that repair station has on other fleets besides its own. And you can get knowledge and expertise from not only the mechanics on the floor but the engineers that support it. This is one of the advantages of going to a specialist. It is kind of like, we've become specialists in the United States all over, in almost every profession -- your profession, doctors, lawyers. ...
But the other wrinkle to this thought, is that a lot of these facilities happen to be offshore, and one of the places we've taken a look at is AMECO. By the way, are they members of your organization?
I believe so. I'd have to check, but I believe so.
OK, tell me what you know about AMECO.
Very little. But I will tell you that it is one of the more modern facilities, obviously, and I'm going to guess because it's in the country that it's in that it has some support from its government to be as efficient as possible because the Southeast Asian area is a big customer draw for the United States.
Have you been there?
No, sir.
The fact that United flies their jumbo jets over to AMECO and has the work done there, does that surprise you? Is that anything unusual? Why would United do that?
Well, I'm going to guess that United looked at the ability to position its aircraft properly to get them there. ... I wouldn't know this specifically, Miles, but I'm going to guess that they don't ground the aircraft for a week and then send them over on that huge flight. They probably position them someplace so that they're closer to that facility, that being beside the point. ...
Well, these were planes that would fly to Beijing anyway. In other words, they've got a maintenance shop in San Francisco; they've got access to one in Beijing. They can do it at either end of the leg, right, and so they choose to do it in China. Why would they do it in China?
Again, I'm guessing that that facility is able to keep up with all of the modern tooling and equipment, housing facility equipment and tooling. I believe that Boeing actually has an agreement with them so they're being trained by Boeing specifically, and they have full Boeing support. And its somebody else's hangar, and it's somebody else's ramp space, and it's -- I mean, I'm a customer over there.
It's a lot cheaper is what you're saying, right?
And it's also more efficient for them. I mean, you can hammer that as much as you want -- it's "cheaper" -- but if the work wasn't being done properly, it wouldn't be cheaper. I'd be taking that aircraft out of service all the time. Do you think that I'd bring it back into the United States to have it on the ground? I'd bring it back to the United States or fly it other places in the world to carry passengers. Safety, as you said. It's not in anybody's best interest to do it cheaper without doing it right.
Why won't they let us in their hangar, though?
Well, I imagine there's a little bit of a trust factor. The news media has not been particularly evenhanded with some of these issues, and I think that there's a trust factor.
But if it's done the way you describe, and it's all to spec, and I've been told you can, you know, eat a meal off the hangar floor, all those things, and they have a great apprenticeship program, and in fact, they actually invited us -- United did -- but we ultimately, a week before we were supposed to go, were told we couldn't. You have to wonder what they're hiding. What are they hiding in that hangar?
You have to wonder. I wouldn't wonder. I mean, I would suggest that --
Well, you get to go in. ... We don't get to go in.
I don't know. I haven't been there.
Well, you could.
I probably could. That's true.
Yeah, but we can't. Why not?
Because they probably trust me to be evenhanded. And just because somebody doesn't want you there doesn't mean that they're hiding something. That's like, why would you hire a lawyer, OK? You must be hiding something to hire a lawyer, right? I mean, I'm not going to buy that.
...
So just shut the door.
Well, that's one way. I mean, it wouldn't necessarily be my way. I'm sitting with you.
OK, but I'm strapping myself to these airplanes, and as a consumer, I'd like to know where it's being fixed and how it's being fixed, and I frankly don't appreciate the fact that the hangar door is shut.
So you think that everybody should be able to go in there.
Not every passenger, but --
Just you.
People with cameras who can tell stories for them. What's the matter with that?
Well, again, if we could trust you enough to tell the story absolutely evenhandedly, you'd probably get more invitations.
So you don't trust me.
I'm going to say that the industry doesn't trust the general media; that's true.
What do you know about ST Aerospace down in Mobile, [Ala.]? Is that one of your members?
No.
They're not?
I don't think so.
OK. Do you know anything about it, what it does in the industry and --?
Well, I know that it's a big airframe facility that works for air carriers.
Right. And their facility is here on U.S. soil.
I think they have two, right? Yeah, one in Mobile, one in San Antonio, [Texas].
Do you know anything about what they do there?
No, besides airframe maintenance, no. Specifically? ...
... Tell me this: At a place like AMECO in Beijing or any place offshore, how often does the FAA [Federal Aviation Administration] drop in?
Well, at least once a year. They can't be renewed. -- they have a sword hanging over their head. They have to be renewed every year. They have to go through a renewal audit every year, foreign repair stations.
And how does that work? Is that an unannounced visit, or is that a "We're coming on Oct. 15, and we'll see you then"?
No, they have to arrange it. Most of that is arranged because they have to actually get into that country, and that's also kind of foolish. I mean, I know people accuse [repair stations] of being able to hide things if it's an announced visit, but since all maintenance has to be recorded, it's kind of hard to hide things because we actually know when somebody is going to show up.
If you have a little advance warning, you can at least tidy up the hangar, maybe move some parts around that are not tagged properly. There's some things that can be done, right?
Sure. That's why we always get findings on those obvious things, because we run around to make sure that we can satisfy that auditor that's coming in. I mean, I don't want --
Explain what you mean by findings. What are you talking about?
When the FAA comes in, or any auditor comes in to audit a facility, they make findings, write down what they find.
Help me understand now. Unannounced inspections: To a layperson, that sounds like a good idea. You just pop in one day and just take a look around. That doesn't happen, does it?
It doesn't happen at, even on U.S. soil, because they found that if you actually get the right people in the facility at the right time with the inspector, then they get the right answers the first time, as opposed to continually maybe get[ting] misinformation or incomplete information. That's one of the reasons that we have a relationship with the agency that works together. The self-disclosure programs and all of those sorts of things are so that we can all work toward improving the systems.
The right answer, or do we want the honest answer?
That would be the right answer.
Well, you say there's a time to get the right answer. It sort of sounds like --
Sometimes they ask questions that take a little digging to be able to answer, so ... it's not like -- some of these are very in-depth audits, and if you ask the wrong person, you're not going to get the complete answer.
So it's a waste of time for the FAA to be popping into these hangars unannounced, in your view?
No, that's not what I said. I said that if we worked together, we can get the right answer. It can be the wrong answer, according to the FAA, but you'll get the complete answer. I didn't say it was a waste of time. You certainly, if you're a knowledgeable inspector, can pop in announced or unannounced and be able to find fault if that's what you're looking for. You'll also be able to find compliances if that's what you're looking for.
But this notion of saying, "We're going to come in two weeks and take a look at your hangar" -- seems like a lot of effort could be made if you're trying to hide things to do just that, right?
Sure. Could hide things all of the time without being told when they were coming. You'd be hiding things from your customers; you'd be hiding things from your auditors all of the time. It's not just the FAA that audits these facilities. It's the airlines; it's other repair stations. I'd be doing a lot of time hiding stuff instead of working. I don't know if I'd make a heck of a lot of money.
I guess what it boils down to is how much visibility do we have inside these hangars. We got none. Does the FAA get enough?
That's a real difficult question for me to answer. I happen to think they do, because I don't think it's the government that forces us to be in compliance. I think that we've got a pretty good economic system that says that if you don't do good work for me in this industry and I have to put my aircraft on the ground because of your work or if I have to do anything, send it back in a just-in-time environment, I'm not going to use you. I mean, if you want to look at it that way, there's 700 maybe repair stations in the world that work continuously for air carriers, and that's because they've proven themselves. I mean, it's interesting that we talk about contract maintenance, and you look at FedEx and UPS, which we don't think of as airlines because they don't fly people. They're one of the few airlines that can't find another air carrier to carry their passengers if something happens to their aircraft, so reliability is very, very important to them, and they contract most of their maintenance.
OK, let's go back and do a little 101 here for a minute. To work on an airplane, what qualifications do you need?
To work on an airplane as an independent individual, which, by the way, you can't do under [Part] 121 for an air carrier, so working for your aircraft, you have to be certificated by the Federal Aviation Administration under Part 65, which is an individual mechanic certificate, and the ratings are Airframe and Powerplant [A&P]. And beyond that, you can't do the work unless you've done it before and been supervised in doing it or be witnessed by the FAA in doing it, and then you have to make a record. All maintenance, preventative maintenance and alterations have to be recorded. And then if you are anything less than a major repair on a small aircraft, you approve it for return to service as -- our shortcut is A&P mechanic. It's actually mechanic with an Airframe and Powerplant rating.
And to get this Airframe and Powerplant rating, the bar is pretty high, isn't it?
You have to go to school. Well, actually it's a license to learn, because the basic requirements are hours as opposed -- and then you have to pass an exam, written and practical exam.
But there's a lot of work that goes into getting that license, isn't there?
Two-year degree.
OK, so it's a two-year degree. And most of the mechanics working for the major legacy carriers have this A&P rating, don't they?
Correct.
What's the percentage? Do you know?
I don't.
OK. But a high number of them do. When you get into the MRO world, the outsource maintenance world, it's a different story, isn't it?
Can be.
OK. Explain what happens there.
The regulations change from an individual certificate to a company certificate. And by the way, this is a choice of the airlines, right? The airlines, for the persons in the hangars that are touching the aircraft and especially during line maintenance, I'm going to say that the majority if not all of them are individual certificates, but the work isn't being done under the individual certificate. It's being done under the air carrier certificate. Just a point of clarification here, because whether or not I have that certificate for the airline, I also have to have the training required by the airline, and it's the same thing in an MRO environment. ...
... In other words, if I work there and I don't have an A&P certificate, what can I do?
You can do everything except approve the aircraft for return to service.
Provided I do the work with supervisory input, right?
No, you don't have to be supervised. The air carrier has to ensure, whether or not you're certificated, Miles, the air carrier has to ensure you know what the hell you're doing. The air carrier has to know, has to ensure you know what you're doing.
Right. So how does the air carrier know that?
Training and testing and experience.
Wait a minute. The air carrier's over here; they send a plane to this place wherever it may be. It's not like --
And now I'm in an MRO environment, or am I in an airline environment still?
You're in the MRO now, the outsource MRO. How do they know, you know -- there are fewer people with the Airframe and Powerplant certification working on the airplanes. How does it work? How do you meet the regulations when you have fewer people that actually are certified to work on the airplane?
OK. Just because I have a certificate doesn't mean I know how to work on that particular aircraft. The air carrier and the repair station both have the responsibility of ensuring that knowledgeable, experienced persons work, ... perform their tasks. And in fact, in the repair station world, I have to have a training program approved by the FAA that ensures each person performing maintenance, preventive maintenance or alteration are capable of performing the assigned task. It's very specific; 145 regulation is very specific.
So, help me. I feel like we're a little in the weeds on this. If you're doing your work in-house at American, a high percentage of those people are licensed to work on the airplane.
And they are also specifically trained by American on American's ways and means of performing maintenance. I can't take somebody out of A&P school and slap them into an airline environment and expect them to know their elbow from their other bodily parts. It just won't happen. And it doesn't happen in the MRO world that I know about. So the individual has to have the knowledge, either through training or experience.
So there is on-the-job training, no matter where you go to work in this business?
Absolutely.
So that means it's important to have supervisors who are watching and mentoring --
And inspectors, and experienced mechanics. I mean, any workforce in a blue-collar environment, that hands-on environment, that experience is pretty important. Now, you have to be careful that they don't get too experienced, because that's when the human factors come in of "Oh, I know what's wrong."
So you don't want too much experience --
You want your experience tempered with a lot of knowledge that you may not know everything.
All right. So when you go into a place like ST, for example, the ratio of people with a license to work on an airplane to those that don't is very different than it is at American. About a third of them actually have that piece of paper from the FAA. In the real world, how does that change the way that plane is fixed?
I'm not sure in the real world it changes the way the plane is fixed. I still have to ensure that the persons are capable of performing the assigned tasks, and I have to know that I have to have -- not only do my individual mechanics have to have that knowledge through either training or experience, but so do my supervisors and inspectors. ...
Miles, you and I can go back and forth about this quite a bit. I mean, the regulations are very clear. You can't have people that don't know their elbows from other bodily parts working on aircraft. The fact that people may try to get around that doesn't change the rule. The rule is there, and the oversight is there, and the capability to oversee a repair station with an approved training program is actually higher in some cases than in an airline environment where it seems to me that you're taking for granted that because somebody's certificated, they actually know something. I wouldn't. I can't do that in the repair station environment, and I can't do it in an airline environment, and you basically couldn't do it as a private pilot.
All things being equal, though, wouldn't you rather have the guy with the certificate, the license, working on your airplane?
No, I would rather have somebody that actually knew what he was doing and the certificated person. ...
Well, the certificate has something to do with that, doesn't it?
Does it? I know a lot of educated idiots. Not sure that the certificate is what -- I mean, I had a certificate when I graduated from law school, and I'm a better lawyer now than I was then. And I was overseen then, and I had a certificate. ...
Part 43 is very specific about how it is supervised and the guy with the license is supposed to witness, supposed to witness the work. And what you have in a lot of these facilities is a ratio of supervisors to workers without licenses which makes it impossible for them to look at all the work that's being done, right?
No, if I am an individual, Part 65 mechanic working under my Part 65 certificate, then the non-certificated person such as myself would have to be directly supervised.
Right.
Not in a l45 or a 121 environment. The purpose of having a business certificate, you know, one step above the individual, is that the business has the training program and the system, the quality system, the layering of the quality system to ensure that only experienced persons work in their area of experience.
But who is policing all of that, that mentoring system?
Well, there's three things that are policing it. The first thing is the repair station's quality assurance department itself. The second is a host of customers, because most air carrier customers, especially on the completed aircraft, not only audit the station before it's used by the air carrier but also during the maintenance they'll have on-site reps; and then a number of civil air authorities.
How much do these guys, starting off -- these contract employees -- how much do they get paid?
I have no idea. I don't keep those economics. I mean, overhaul and maintenance might.
Do you make more or less than being a car mechanic or plumber? Where does it stand in the scale of things?
I don't know.
You have no idea. Really? You don't know?
I don't know.
You must know. Come on.
I have no idea.
All right. The work that is done there, is it every bit the same quality that would be done in a facility run by an airline with the majority of the people with those certificates to do the work?
Absolutely.
How can you be certain, though?
Well, not only does the rule require it, but the safety record shows it.
And the safety record does, I guess, speak for itself.
It's supposed to, but apparently it has to have a lot of people speaking for it. Must be an awful soft voice that it's speaking in.
Well, maybe we take such things for granted too much unintentionally. I don't know.
Well, that's true.
One of the things that comes up as well is language. … The manuals are in English, and many of the workers involved in this business, either here in the U.S. or certainly offshore, don't speak English as a first language and don't have the skills frankly to read that manual and understand the work.
How do you know that?
Well, we've got plenty of people attesting to that fact.
OK. So we have subjective evidence of that?
Yeah, there's plenty of subjective evidence of that. It's difficult to quantify and pin down, as you well know. But the point is -- why don't we just back up? How important is it to be able to speak English to work on an airplane?
I don't think it's important to speak English, but again --
Read a Boeing manual --
That's not speaking; that's read, write and understand the English language is actually the requirement for all inspectors. Supervisors in the United States have to be certificated, so they also have to speak the language. But read, write and understand is a requirement for all inspectors and supervisors. The other thing that I would just point out here, and we haven't had a chance to really study this, but it is one of the things that we're working on is English proficiency here at the Aeronautical Repair Station Association [ARSA], because, as you pointed out, we don't have a corner on this one. I mean, the United States has got its own issues with English as a second language, so we're working on a standard, a technical, to make sure they do understand technical instructions.
So it is important --
I think it is important, absolutely.
The fact that you're working on this, does this recognize that there is a problem here and how much of a problem is it?
It recognizes that we have to answer the question of whether or not it is a problem, and the only way you answer the question of whether it is a problem is to make sure we establish a standard and that people can meet it. Again, Miles, we've got to look at the fact that a lot of these instructions are translated from English into the country location's language, and also the air carrier itself has translated them into work cards and other documents, and there's a constant communication on it.
Right. But that's not what the regulation says. The regulation says "understand English," right?
The regulation says -- remember, again, this is for inspectors and supervisors -- they have to be able to read, write and understand the English language. It's ironic. Look, you're not going to get an argument from me that we have to address this issue, and we have to address it worldwide, and it's ironic to me that for pilots English is a required language, but it isn't for the rest of the industry.
So this needs to get fixed.
This needs to be addressed. I'm not sure we're fixing the problem.
Don't you want to fix it?
I think it needs to be addressed. When you identify something and we don't have an answer doesn't necessarily mean it's a problem. It means that we need to address it and answer it. If it was a problem, Miles, would we have the safety record? I mean, we keep saying that the safety record speaks for itself, but when you attack it, making me or anybody else in our industry prove a negative, it's kind of hard to see if you're going to be balanced.
Well, here's the thing. You're right. The safety record is indisputable, that it is a safe way to get from Point A to Point B. There's no question.
The safest way.
Ever devised by human beings, all right? OK? But the concern that we see and is that we have an industry that is under economic stress and --
Miles, it's been under economic stress for years. ... Help me understand when the airlines haven't been under economic stress since deregulation.
Since Kitty Hawk, [N.C., the site of Orville and Wilbur Wright's first successful flight]. ...
And we work every day, year, month -- everything -- to make it better and better and better, through design, through operations, through training pilots, through training. ... It's interesting that we have to continually defend it so vigorously. Do we have areas that we need to address and improve on? Absolutely. ...
Does the absence of accidents necessarily mean things are as safe as ever?
Well, the absence of accidents proves that we have increased our safety record. The fact that we continue to work to improve it even more is an industrial thing that we've done forever. Look, you want economic pressure? Go out and have more accidents. Then you'll have economic pressure. You talk about cutting corners. It's not going to be in the safety arena that you cut corners. If you do, you're an idiot. You just can't. This isn't your car. You can't ignore the maintenance, because then your aircraft won't fly or something will happen to it. And in both cases, you're going to be under more economic stress. ...
We've established that contract maintenance is a lot cheaper for the airlines, OK?
It's much more economically viable for the airlines because they send it to specialists.
Isn't it better for the airlines to fix their own planes?
Why would it be better for the airlines to fix their own planes if it can be done less expensively, more by specialists? Do you fix your own car?
No, I don't. But it's not going to fall out of the sky when I'm driving down the street, you know.
No, it will just kill somebody, most likely you, and some old lady on the street. Then we'll be doing the story about you.
... The point is, what entity knows better and can provide the level of detail and understanding about this aircraft than the airline itself?
Well, the manufacturers would say it would be the manufacturers, which is one of the reasons that they have 60 percent of the maintenance market, is obviously they do and are able to do it much more efficiently. And in fact, in the engine environment, as you know from your own research, I'm sure, the manufacturer is the one that has the majority of that market. So I'm not sure that it is always the airline. You know, again, if you go to Europe, which took our model here in the United States and improved on it, if you will, they would tell you that air carriers shouldn't, cannot do their own maintenance. It has to be a 145 repair station, and that l45 repair station has to have a quality assurance system and has to respond to the customer and to the findings on the aircraft. This isn't about who knows better; this is about doing it right. We don't wake up in the morning in this industry saying, "Jeez, we're going to do it wrong."
All right. So you're doing it right. All these shops are squeaky clean and perfect, and all the workers are singing and whistling all day long because it's wonderful to work there. You have the power. Can you get us into one of these hangars?
I will certainly ask around, Miles. But I, you know -- we -- they don't trust you, and it's part of that cynicism that you just showed me.
Cynicism? I'm just asking questions. Listen, I'm flying these planes a lot. I want to know who is fixing them. I want to know if they can read the manual. I want to know if they've had their background properly checked. I want to know if they're sober. I want to know how many hours they've worked. All of these things are completely obtuse because there is this shroud around this, and the airlines don't seem to want us to know that this is happening. I can't understand why.
Sweetheart, how are the airlines not letting you -- they let you into the MRO. The airlines themselves --
No, they didn't let us in. They didn't let us in.
Yes, they did.
Oh, to the convention?
Jiminy dang Christmas. Try 20 years ago, try to get in there. You know, we're just a little bit more trusting here.
So just the fact that I got into the convention is a big deal? Really?
It is actually a big step. You know that.
Well, once I saw the follow-me girls, I knew I had arrived. But having said that, that doesn't really tell me much about what they're doing to the plane I'm flying on, and I want to know.
Why? But why? I mean, you wouldn't want --
What do you mean, why? Why wouldn't you want to know?
Why do you want to know now? Because there's questions? Because it's done on foreign property? I mean, because if you look at the increase in maintenance in the dollars, I mean, it's only 2 percent in a year. I mean, OIG's [Office of Inspector General's] report just kind of showed it [to be] about 2 percent a year increase in contracting, and if we looked at any other industry, I imagine it's a huge -- I mean, it's a bigger jump.
... It seems to me that the flying public, the consumer, does have a right to understand how this works, and for whatever reason, the door is locked. Why is the door locked?
Knowing how it works and being able to enter into private property are two different things. You can find out how it works. I mean, in some cases, people are thinking it's kind of like being invited into an operating room, you know what I mean?
I could get into an operating room if I scrubbed down, you know? I mean, seriously.
Only if the customer allowed you.
So the customer has a problem?
Some customers absolutely have a problem, and some of the repair stations have a problem. You can't get me any closer to the truth on this one, love. I am telling you the truth.
Well, what is the truth? I mean, I have to take it on faith. I have to take it on faith that everyone is squeaky clean and great, right?
No, the truth is that they don't trust that attitude, that you would give them a real clear shot and express their showing honestly.
But you're going to try for me, right?
I will try.
Let's talk about the FAA for a minute. How would you grade the FAA on policing maintenance in general in the airline business?
Oh, they'll get a B-minus.
Minus. Tell me.
Well, the first thing is that it's not their job to police maintenance. It's their job to police compliance with the regulations, and I know that this is a thin line I'm trying to walk here, but it's my job as a certificate holder to not only comply with the Federal Aviation Regulations [FARs] but my contracts, which tend to have a more strict standard for exactly what my customer wants. So the FAA really needs to understand that the clearer that it writes its regulations and the clearer that it writes its guidance material, the less time we can all spend on nonessential issues.
So the FAA is not giving clear marching orders. We've heard this time and again. They tend to -- they write regulations which confuse people and make them put wire harnesses in backward and so forth.
Well, I mean, that's a technical thing that I think that the manufacturers could have --
Actually, the manufacturer might have been involved in that one, too.
-- shared a little bit. But it's also us in the industry obviously under the regulation, under the United States regulatory process, we have a chance to comment on notices of proposed rule making, and sometimes we don't. And we don't do it clearly, and we don't explain to the agency exactly what it would take to be clear. We tend to do a lot of negative feedback without any alternatives, kind of if you're not part of the solution, you're part of the problem. And rule making has become a very cumbersome project for both the government and the regulated parties -- individuals, pilots. They're going to raise your requirements. ...
But just to be clear, the FAA , the inspectors that go into these shops, they're not out there touching the metal, as it were, right?
They can, but that's not the government's job. The government's job is to ensure my certificate holders know how to touch that metal properly. I mean, we've moved from very, very knowledgeable inspectors that knew about the aircraft to system reviewers and integrators, auditors. I mean, there's a whole complaint internally at the FAA by the inspectors' union and also by the mechanics and everybody that we've moved [that] we're not as blue-collar about our approach, that I should know how to fix the aircraft if I'm an inspector. No, you should know how to question the person that is inspecting the aircraft or working on the aircraft to make sure they know what they're doing. This is a step back that we have taken as both the industry and the agencies for quite sometime. I mean, that happened 15 years ago whether we recognized it or not.
So the typical FAA inspector doesn't necessarily know how to fix an airplane.
Correct. Well, that particular airplane.
They know how to manage paperwork is what they do. They make sure the boxes have been checked.
They should know the regulations -- what the regulations require and what the certificate holder needs to do to be able to show compliance. They're not just paper shufflers. They have a much more sophisticated role than that.
But this notion that people might have, that the FAA inspector is kind of looking over the shoulder of work being done, that doesn't happen.
That stopped in the '50s. I mean, if you go back to the Civil Air aeronautics Regulations [CARs] that started [in] the Department of Commerce in the '20s, the FAA actually approved aircraft for return to service after the work was performed. That stopped in the '50s. They recognized then that there was going to be too many aircraft for the FAA to have that kind of a hands-on role. ...
So basically we rely on the industry to police itself, right?
We basically rely on good businessmen to understand that if they don't do the job right, they're not going to be in business for very long. You know, there's rules out there, Miles. And you know, it's like everybody that's, like, speeding on the highway. Everybody speeds, but it's somebody's fault when they get caught. No, this is an industry that depends on absolutely knowing what the heck I'm doing, and I'd better know or I'm not going to be in business very long. I won't get reliability; I won't give good service. This is industry as a whole. You want to go out and find people that are doing it wrong, which I'm sure you do.
... I know you don't know ST [Aerospace Mobile] specifically, but I want to just run through some of the things that some of the workers there told us, anonymously. They talked extensively about a shortage of qualified mechanics. We've talked about that a little bit. Extensive problems with the English issue. About quality control being not enough, not adequate, an afterthought. Matter of fact, the ratio of quality control inspectors to workers was 80-to-1 -- 80 workers to 1 quality control inspector. They talk about problems with tagging and identifying parts, using expired parts. And then they talk about a general sense of not providing the proper resources at a senior level, the management there. When you start adding all that up, what you find is an aviation maintenance sweatshop practically. It doesn't sound as safe as it should be.
Well, OK, jeez, when did you stop beating your wife? Look, Miles, none of this -- apparently even you -- this isn't objective evidence. It sounds like people are complaining. I don't know why they're complaining.
Well, why would they? They're putting their jobs on the line, frankly, talking to us.
How are they putting their jobs on the line when they're anonymous?
Well, it's still a risk.
Is it? You going to tell people?
Am I going to tell people what?
Are you going to tell people who you talked to?
No, we protect our sources, but, I mean, these are people --
OK. So help me understand how they're still at risk.
Just coming to talk about something like this when your job is -- let's move on from this. This is what they told us.
It's unsubstantiated. This is like convicting somebody in the media. Yeah, I'm not going to do it. I'm not going to do it to ST or anybody else. We don't know. We don't know. ...
Well, why would they tell us if it isn't happening?
I have no idea. Do you?
Would they make it all up?
They might. Who knows? I'm not going to comment on it. Unless you bring me proof positive that this is actually what's taking place, I don't think you know, and I don't think I know. I know I don't know. I'm not going to take disgruntled employees or people that will talk to the news media anonymously when there's actually whistleblower protection laws that would allow them to come forth if they wanted to without retaliation, at their word. I just won't do it, and I don't think you should either.
If somebody said that and attached their name to it and that was the description of that facility, what would you say about that facility?
I would say that the FAA better get its butt in there, because it will be pretty obvious that it shouldn't hold a certificate.
There's advance warning, enough [time] to clean things up.
How can they clean all that up? How can they clean all of that up? How could anybody possibly clean all of that up?
I guess that would be a big job.
I think that what we have to do is be careful of where we throw rocks. I don't think that anybody has the corner on safety, and I think that we have to work every day to improve, it and I think that in this industry, I'm particularly upset at people who would continue to work there. If this is truly what it is and you're hearing it from somebody that is a supervisor and has authority, then he'd better not work there, or she. There's a shortage of workers out there, Miles. Why aren't they working for somebody else?
Editors' Note: Miles O'Brien hands Sarah MacLeod FAA inspection reports of ST Aerospace Mobile that show FAA inspectors finding some of the same problems mechanics spoke to FRONTLINE about.
... It goes to your point that you were saying, you know: You're getting a bunch of anecdotal people with axes to grind when in fact there is some documentation to support that there are problems at a facility like this. And I guess when you combine what we heard with what's in these documents, the picture is not very pretty, and it doesn't speak to safety when I look at it.
OK, Miles. I mean, look, auditing and inspections do find things that need to be addressed, whether they are as extensive or as sharp as first reported. That's why you have to look. That's why the company has a chance to respond. That's why the FAA and the airline will go in and look.
Shortage of qualified maintenance personnel; ratio of quality control inspectors: These are all the points that we were talking --
Right. That we were talking about earlier. But you have to look at what were the qualifications of the individuals that were being overseen and the qualifications of the supervisor; that you can't look at any of this in a vacuum, and you can't look at it on the assertion of one person. You know, even criminals get -- eyewitnesses have to be supported by objective evidence.
Well, OK. I mean, we've got lots of workers telling us this story; we've got documentation. What's it going to take for you to believe that this may be what's going on inside that facility?
I don't know. I mean, the first thing is, is that let's see if the FAA adjudicates it -- I mean actually brings charges and adjudicates it; has a notice of proposed civil penalty, you know. Has America -- I'm sorry, the customer -- addressed it? ...
There's always two sides to the story. Always. You might not want to accept the other side, but there's always two sides.
Give me the other side here. What is it?
I don't know what it is, because I'm not at the facility.
Is this a facility that is trying to wring out as much cost as possible in order to make a profit?
Look, there is no facility that wants to be viewed by you negatively, viewed by the FAA or its customers negatively. There is no facility that I know of, Miles, that would want that. That's number one. And number two, there's no facility that is going to get away with shoddy work for any length of time. You do not get reliability out of shoddy work, and people do not come back, and you're not successful. You're not successful. You either have to redo the work or you're out of business, because you can't pay for the downtime of the aircraft.
The problem is --
-- that you have accusations in front of you that you want somebody to answer, and I'm not the one that's going to be able to do it. I just can't do it.
Editors' Note: Read ST Mobile's reponses to FRONTLINE's questions here.
The possibilities exist that the airlines trying to save this money are receiving planes back that aren't fixed properly and they don't know. How could they possibly know?
That the plane doesn't work? ...
But given that there is less transparency as to what goes in these facilities --
Really, you've been inside of Boeing when a plane's being made --
I'm not talking about Boeing; I'm talking about ST.
OK, but you said less transparency. Look, the aviation industry has a very complicated, long-term industry that has striven for what, 50 years that the FAA's been around, to improve -- it's improved its safety record, OK? You're going to find that people are occasionally doing things wrong? Yes. You're going to find it in every industry.
A lot of people would tell you, though, yeah, it did improve for a long time, but it's at the very least plateaued in recent years.
Well, we did get a lot of that low-hanging fruit -- pilots and design issues. But we're at what, 98 percent, 99.8 percent, something like that? Safe. Yeah. We'll keep striving....
You've had a chance to see this. You've heard what people have said. This is serious if what is in here is true, right?
I don't know that. What's the result of this? What you guys are asking me to say is whether if a facility is so slipshod that it's systemically bad, systemically doesn't have enough workers, etc., then, yes, the FAA needs to take steps. That is its job as an agency.
How often does it do that, though?
Well, it's doing it a heck of a lot more often now. Have you been reading their press releases?
How frequently do they pull a certificate for --?
That I can't tell you. There's a lot of voluntary cessation of operations until the FAA is satisfied.
But yanking a certificate for a maintenance operation, that doesn't happen, does it?
Sure it does.
How often?
I don't know that, Miles. I don't know that as a comparison, because you have to give me a comparison. So I don't know that. I will tell you that the air carrier is going to be on them, and the FAA is going to be on them.
And the FAA does --
Has the authority to pop up at the air carrier and the repair station if the allegations are true. I mean, the air carrier cannot fly an unairworthy aircraft, and the repair station cannot do unairworthy work. Them's the rules.
And when they get that plane back, they, at least at a certain level, have to take it as an article of faith that the work was done properly, right?
Well, they don't have to take it as an article of faith. The regulations would require that the person performing the maintenance must perform it properly.
... Since 2003, thus far, the enforcement from the FAA at ST amounts to an $11,000 fine. That doesn't sound like much.
OK. So that means to me that the FAA was not able to meet its burden of proof, and its burden of proof is a preponderance of the evidence, and that's 50.1 percent. So the proof of the pudding is in the eating. If they said if there was unqualified [personnel], and in fact there were qualified personnel, then ... somebody wasn't able to make the case that they were unqualified. I mean, the FAA doesn't have a huge burden of proof when it comes to allegations of violations, more likely than not, and then the burden shifts to the certificate holder to prove the FAA wrong. So if the FAA is proven wrong, it needs to pick up its bag and go home.
Is the FAA aggressive enough in its enforcement?
Boy. OK, so people don't call me when they're having a good day, so to me they're aggressive enough in their enforcement. The question is, are they enforcing against the right areas? And that would be the question that I would ask. Sometimes they chase things that are less important than others -- not the examples, for instance, that you may be providing, because unqualified personnel, for instance, is something I would like them to take a look at, but if they can't prove it by a preponderance of the evidence, that means that the guy wasn't qualified. It's not that hard to determine.
So you'd like the FAA to look into this more, not just at this one facility but in general?
I would like the FAA to focus on the things that the industry and the public are interested in. Am I using qualified personnel? Does a qualified personnel make me more efficient, make sure that I can get the job done best, right, the first time? Don't have warranty returns, don't have a whole lot of other problems. So if that's an area that needs to be looked at, then yeah, ARSA would welcome things like that. It makes us more efficient, Miles.
Can you give me an example of something they go after that you say would be ... less important?
... All the regulations are important when they lead out to establishing that I have done my work properly. But if you're chasing "I didn't quite make the record the way I, the FAA inspector, would have written down the record," those are the sort of things that bother me the most. Mechanics aren't necessarily the best at writing things down properly. That's not where their expertise lies. So I tend to see the FAA sometimes, you mentioned earlier, kind of paper-pushing things because they're easier to find.
Can't-see-the-forest-for-the-trees kind of stuff.
Yeah, and I think that they do have a lot of pressure on them. FAA inspectors have a lot of pressure on them. They have a lot of certificate holders to review. They've got national standards of what they're supposed to look at. I think that there's a tendency to want to get through the day sometimes, and they're a little bit demoralized from being beat up as much as they have been from Congress and the media and others.
Do we need more of them?
Yes, we do.
How many more of them?
Now, that one I'm not going to be able to answer again, because there's kind of a floating tide of attrition and things like that. I'd also like to see more inspectors and better-educated inspectors. I think that I'm hoping that this next step in the Safety Management Systems [SMS] and others will force us into being better auditors and really being able to see where the risks lie.
Do you have a number of inspectors that you think would be appropriate?
No, I don't. I'm sorry. Because I think we need to balance it against where we should be looking, for instance, in the general aviation population, which has got high numbers of pilots and mechanics and less inspection, not that it's any less safe. I mean, it is an area that we're going to have to start looking at with more frequency, you know, because as the safety record goes up, it's harder and harder to find the things that will fix it, and there's not as many easy bullets , you know, silver bullets.
What happened at the FAA that allowed the workforce to be less competent and for that matter not big enough? Was there just not enough attention paid to this over the years?
Well, you know, we have a lot of unfunded mandates slammed on us by Congress. I guess when I say "us," all the FAA wouldn't appreciate me calling -- being part of them. There's a lot of things that Congress is saying: aging aircraft inspections. I mean, they start dictating what the agency should do in the FAA reauthorization legislation, for instance, but they don't get the money to do it. And it's the same thing the states bitch about, right? Sorry, complain about. And I think that the Congress in some ways doesn't quite understand the agency's role. I mean, it is an executive branch agency, and it's the Congress that gets them the money to do the thing, so I don't think they might understand it and may not trust their agencies. You know, there's a general mistrust about nowadays....
If everybody's policing themselves, what is the FAA's job?
OK. So the FAA's job as dictated to it by Congress is to pass regulations that ensure the highest level of safety when it comes to commercial operations. Without the government agency to put those boundaries on itself and the industry, ... we wouldn't have the assurance, if you will, that everybody had a level playing field when it comes to regulatory compliance.
Let's assume for a moment that there wasn't an FAA. Would the industry be safe?
I'm a disciple of Ayn Rand --
Yeah, Atlas Shrugged and the FAA, we don't need them. ...
Look, everything is a blessing and a curse. With the people that are going to do it right, do it right -- absolutely. Are the people that are going to do it wrong continue to do it wrong or get away with it any better? Probably. Just because there's a cop on the beat doesn't mean that we don't have people that need to be overseen, and vice versa.
Is it harder to do that job the way the business has evolved?
No, I don't think it's harder -- you mean the aviation safety inspector's job?
Is it harder just in general to understand what is going on when you have so many maintenance facilities in so many far-flung places?
No. Remember, we haven't really grown in numbers as much as we have shifted the maintenance around to other places. So just be aware that there's only so many aircraft out there and so many maintenance facilities that can be full and profitable. So we're moving aircraft around. So, no, for the regulator to understand its role is becoming harder because it has more detractors. It didn't always have Congress to beating it up. It didn't always have the media beating it up. It didn't always have internal strife, because the -- there's more management-labor disputes. So I think that the whole economic reality of the world has become more complex as opposed to just the role of the aviation safety inspector. I don't think it is more difficult.
It isn't easier if it's just right there in Dallas-Fort Worth as opposed to Beijing?
No, I don't think it is, because remember, now we are dealing with the Beijing facility has to follow the civil air rules of China and the civil air rules of the FAA and any other country from whom they are performing maintenance. It's more difficult for the facility in Beijing, but for the aviation safety inspector, he's looking at FAA compliance issues. It, she, they. He or she.
He or she gets to pop in once a year after weeks of --
Honey, he can go there anytime he wants to.
Well, it's not quite as easy as that. You know that.
But it's not the air agency that's stopping him from coming in. I mean, believe it or not, we do have State Department considerations that have nothing to do with us.
Whatever the reasons, it's not like just driving down the access road and popping in the hangar. It doesn't happen that way.
Correct. So are we assuming that -- I mean, again, you're coming from an assumption that they're doing it wrong until the aviation safety inspector shows up, and the layers of protection in our industry are much stronger than that.
So, having the license, what does that --?
Having the license shows that somebody had the discipline to go through the process, the two years of school, and I can't remember the number of hours. It shows a certain amount of discipline, and I think that's a very positive thing. I'm not trying to take away from people that have certificates. What I am saying is that because I have a certificate doesn't mean that you can assume I know anything about fixing that aircraft in that hangar. Most licensed mechanics will honestly tell you that the license was a license to learn.
And when I got my pilot's license, that's what they told me. This is a license to learn. But you can't fly a plane without a license. Shouldn't it be the same for the person who is working on the plane? Shouldn't they be licensed?
The way the industry has developed from the '50s, a repair station is the licensed person. That's the person that's responsible for approving the aircraft for return to service or approving the work for return to service. And even as a licensed person - remember there's other people that can sign the records as opposed to doing the work -- an individual mechanic out there in Fredericksburg, [Va.,] can have three or four people that he's overseeing, and it's overseeing to the extent necessary to ensure that they're performing the work properly. So if I a have a very experienced helper, I don't have to directly oversee them every step of the way, even as an individual mechanic. All I'm trying to say about all of this, Miles, is that it's very -- experience is to me more important than the license. The license starts you. It proves that you have discipline. There's other ways to prove that.
Still, wouldn't it be better if everybody had their license? Or is that just impractical? Is that an impractical notion these days?
Not necessarily. The first question: Would it improve if everybody had a license? Not necessarily. I don't know that a government blessing makes me any better. I think that if I'm a specialist in a machine shop or if I'm a avionic person or if I'm only doing certain services like braising, I don't think I need a license. Actually, I have to have a certificate from society at that point. Those are really volunteer standards.
So when you're out there in the job market and trying to get experienced people, what does a well-qualified, experienced mechanic earn?
I have no idea.
Oh, that's right. You told me that. You don't know that. But when you're getting close to the minimum wage, what kind of experience levels can you anticipate?
I'm not qualified to answer that question, but there's certainly a lot of human resource studies that show that the amount I get paid is not as important as other things, in my job satisfaction, so I'm very leery of this "Jeez, if you get 'em cheap, you must not be getting 'em good." I think that's an individual integrity issue that I don't know where any of us are qualified to answer. It's like I said to you earlier, you're probably not getting paid as much as [60 Minutes correspondent] Lesley Stahl, but I think you're probably just as good.
Well, but what's kind of interesting is that at ST, the pay is such that they are able to fly workers in from Asia who are willing to work at that wage.
Well, see, again, I don't know what that wage is, but it seems to me that flights from Asia would cost them something, so --
Well, it's still cheaper for them to fill up that factory --
Or we're not getting qualified individuals in the United States. A lot of us are not encouraging our people and our children to go into blue-collar work.
... Supply and demand. If you paid a little more, that would solve the shortage problem, wouldn't it?
You think? I don't think, for one thing, we don't teach shop in school anymore. We are not training our children to be blue-collar workers, so I do not subscribe to the argument that if I paid people more, they would go into it, because you are, you as parents -- I'm not lucky enough to have children, or unlucky; I'm not sure which -- but not very many people are going into blue-collar work, and, in fact, you're kind of discouraged from it, and you're looked down upon for being blue-collar. Go listen to country-western music for a while.
But having said all that, at $12 to $15 hour, that guarantees that nobody's going to be interested in doing it, right?
Maybe in Washington, D.C., but there's certainly areas in this country where the cost of living is such that you can get good workers at less than that.
Well, they can't even fill up the factory in Mobile, [Ala.,] with local workers.
Sweetheart, it still may be because they're not qualified in Mobile. There's very few blue-collar trades right now that aren't screaming because they have shortages -- diesel mechanics of Caterpillar tractors, any of these blue-collar trades.
It has nothing to do with what you pay.
I will say it has less to do with what you pay than it has to do with what we encourage in this country, as a nation, and we look down on blue-collar workers.
You get what you pay for, right?
I'm not going to agree with that. I'm not going to charge as much in this trade association as other trade associations charge, and I give better service. You aren't being paid as much as other reporters are getting paid. Are you giving less service? I think that is undermining the entire integrity of the workforce.
... And the work that's being done on that airplane is just as good as ever.
Absolutely.
Even at $12 or $15 an hour and fewer licensed mechanics, all those things.
Yes, sir. I mean, you keep saying it: Our record stands for itself. You'd think that was -- you keep thinking that it's by accident apparently. This is by design. We designed the system properly, and we will continue to improve that design.
And we're not pushing that system too far here?
I don't believe so.
This information on the companies that provide these services to the airlines -- we go to the FAA; we ask for it. They say it's not public document; you can't see it. And it goes back to what we've been saying about the hangar door being shut and nobody letting us in. Why is that not something I should know about? I should know who's doing the work, shouldn't I?
... I guess what I would say is that these are contractual relationships, and no one -- my people and the airlines aren't obligated to tell the public what they have contracted, who they are contracting with for food or anything else.
But as a consumer, as somebody who gets on that airplane, [it would] be nice to know that the airline I'm flying uses a maintenance facility that I'm comfortable with, but I have no way of knowing any of this.
You're comfortable with, as opposed to a maintenance facility that what? You're uncomfortable with?
Well, I don't know that I'd be very comfortable with flying on an airplane that came out of a facility that generated all this.
If you pull that from the airline itself, the airline maintenance itself, would you feel comfortable flying the airline? Is that what you [are] wanting as a consumer, is all of the information possible about the business relationship --?
I just want a little transparency, that's all. That's all anybody wants, is to understand what's going on in the system. The system seems to be designed to keep us in the dark, and I don't know why.
The system is a complicated regulated system. It's regulated. See, at some point, I was talking earlier about trust, why you and I are sitting down, even though I frankly don't trust you to do this balanced. I will sit down with you because I think it's important that there be some understanding of it, but this is an industry that took me 30 years to understand. I'm not sure that the consumer, whether you had the right or not, whether they would understand it if it was presented to them. You just want.
Well, I think you could give them a little more credit than that. They might get to understand --
Well, then I think you might want to go look over the shoulder of your mechanic the next time he's fixing your car that you can't even find the dipstick on anymore because it's so run by computers.
But I can do that if I want.
Yeah, and if you owned an airline or an aircraft, you could do it. But you don't own an aircraft. You're just buying space on them.
But I don't know what I'm buying.
Sure you do. You're buying the safest form of transportation that you can buy at the cheapest price you can bloody buy it.
Yeah, but is it --?
You want more? Fly your own aircraft and be less safe. …
COMMENTS
blog comments powered by DisqusIn order to foster a civil and literate discussion that respects all participants, FRONTLINE has the following guidelines for commentary. By submitting comments here, you are consenting to these rules:
Readers' comments that include profanity, obscenity, personal attacks, harassment, or are defamatory, sexist, racist, violate a third party's right to privacy, or are otherwise inappropriate, will be removed. Entries that are unsigned or are "signed" by someone other than the actual author will be removed. We reserve the right to not post comments that are more than 400 words. We will take steps to block users who repeatedly violate our commenting rules, terms of use, or privacy policies. You are fully responsible for your comments.